If you have specific application requirements, or cannot find a standard electronic enclosure to meet your exact needs, you may need to work with an electronic enclosure manufacturer to create a custom enclosure for your project.
Here are some key points that will help make your custom enclosure project go more smoothly.
- Start with an idea of the type of enclosure you need. (See guide below.)
- If you need a custom dimension or other structural change, look to a stock enclosure for inspiration.
- Customizing a stock enclosure usually saves time and money.
- A fully custom enclosure gives you freedom to design exactly what the application requires.
- Metal enclosures are the most cost effective to create from scratch.
- Enclosures made of plastic or fiberglass require completely new tooling that may be costly, so custom molded enclosures are best in high quantity.
What is the Difference Between a Modified Enclosure and a Custom Enclosure?
There’s no reason to invest in a custom electronic enclosure if you can modify a stock enclosure to meet your application’s requirements. Nevertheless, the decision isn’t always easy. The information below will help you weigh the benefits and drawbacks of each approach. You may even discover a few surprises.
Custom Electronic Enclosures
A custom electronic enclosure is defined as being completely developed from scratch and is mostly used when a suitable solution cannot be found off the shelf. This allows for a very specific visual look of the enclosure as well as exactly meeting the needed dimensions and functionality.
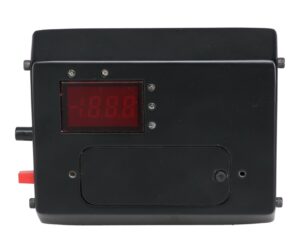
Bud can help with the electronic enclosure design and creation of a from-scratch enclosure, starting by understanding the application, then working with CAD tools to arrive at an ideal enclosure design. There is a lot to keep in mind, such as allowing space for cabling, planning how PCBs will be mounted, the location of power supplies, tolerances and drafting angles, and heat dissipation. Our experience can help prevent costly design mistakes.
More often the inspiration for a custom enclosure is a standard product. A designer may like a particular electronic enclosure box but need it in different dimensions or need a hinged cover on a stock enclosure that is available with only a screw-down cover. A common request is a special formulation of plastic, such as adding UV protection to an enclosure that was designed for use indoors. Basing a custom design on a standard enclosure provides a fast and cost-effective solution, because much of the engineering has already been worked out.
In addition to supplying custom-molded plastic enclosures, Bud can fabricate custom metal racks and sheet metal enclosures. Our factory has the machinery and skilled workers needed to form and weld almost any design of steel or aluminum enclosure. Making custom industrial enclosures in steel and aluminum is more popular than in other materials because tooling costs are relatively low.
The closer to a manufacturer’s standard enclosure the custom enclosure can be, then the more cost-effective it can be. A good example is a custom server rack we developed for an internet service company that had a specific assembly, weight load, and seismic needs. We used a standard Bud rack, slightly changed several dimensions, and upgraded it with extra welds, different gauge steel, and doors that were removable in a specific way that met the application’s needs. We performed seismic tests for them, simulating their equipment installed. The end product was a totally custom rack that still used many of the standard Bud design and production techniques.
Custom plastic or die-cast aluminum enclosures with dimensional changes are often significantly more expensive, as tooling costs can be quite high. The benefit of a new tool is that it is easy to design-in special features such as additional mounting bosses, wall-mounting provisions, card guides, as well as cutouts and holes that make the enclosure a turnkey unit. If the quantities are significant, the tooling charges are easily amortized, and so will allow for a unique looking product or one that meets the specific customer need. We have done this for several end-products offered by a wi-fi provider who had specific needs to make the box attractively mesh with the surroundings and contain easy installation features.
Other customizations for a plastic enclosure might include changing the plastic to allow for different colors, added UV protection, or flammability protection. If a standard size box is chosen, sometimes these changes will not require new tooling, which makes it a very reasonable shift.
Extruded aluminum enclosures typically have a fixed height and width but can readily be varied by depth. Changes in the fixed dimensions will require a new tool, although extrusion tooling is often not expensive.
Modified Enclosures
No conversation about custom enclosures is complete without discussing modified enclosures. A modified enclosure is a standard, off-the-shelf enclosure that can have features or functions added to it, using proper machinery or tools. The most common modifications are made to enclosures by cutting holes, slots, or cutouts. Most enclosures must be modified because they need to allow for input or output of power or data such as with front panel custom cut-outs for displays, switches, buttons, or signal wires… at minimum an opening for a power cable.
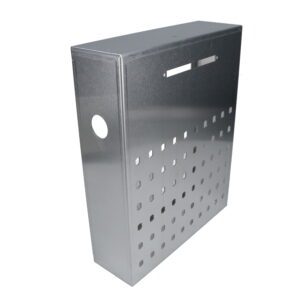
Some of these changes are functional, such as a special gasket that provides EMI protection. Some of these changes are cosmetic, such as digital printing and special colors intended to make the end product stand out in the marketplace.
Not really a modification, but along the same lines, is pre-assembly. Racks can be shipped with customer-specified configurations of accessories such as shelves, fan trays, cable organizers, and chassis. Electronic enclosures can be pre-assembled with accessories such as standoffs, internal panels, and vents. Bud will even drop ship such enclosures directly to your CM, streamlining the supply chain, simplifying installation, and saving time.
With a modified enclosure, the basic enclosure—its structure—does not change. Because there are so many families of enclosures, in so many sizes and shapes, usually design engineers can select a standard enclosure that will do the job with minor modifications. Bud offers around 3,000 different models of enclosures.
Starting with a stock enclosure is obviously more cost effective and much faster than ordering a custom enclosure that must go through an entire design, manufacturing, and shipping cycle. Many injection-molded enclosures are made in Asia, which lengthens the delivery time by several weeks or longer. In contrast, about 93% of Bud’s inventory is available for same-day delivery.
Ratings are another consideration. It’s easier to get a UL NEMA rating on a modified enclosure if the original box is NEMA rated.
Many of the electronic products that consumers touch are housed in enclosures that we don’t notice are actually stock enclosures. Enclosures used for medical devices, industrial tablet PCs, and hand-held remote controls come in so many variations that people don’t notice the enclosure is not custom. This is especially true of enclosures that are printed with logos and carry branded colors.
Considerations of Custom Electronic Enclosures
The decision to create a custom enclosure needs to consider the timeline. It takes time to develop detailed CAD drawings, to acquire or modify tooling, and to meet any certifications. A UL rating can take up to six months to obtain and longer if design changes are needed.
Another consideration is quantity. If tooling for a custom plastic enclosure costs $15-$60 thousand, then running only 100 pieces may not be economical. If instead the run is 100,000 pieces, then customization may be worth the cost because the enclosure can be designed to speed assembly, simplify maintenance of the end product, and match the look of the brand.
Even when customizing an off-the-shelf enclosure, experience matters. For example, welding on a lock or a hinge may change the tolerances of the enclosure. Also, there are minimum clearances for cutouts and mounts, such as the distance from an edge or corner. The impact of design changes must be understood so PCBs, cables, and other components fit as expected. Having Bud as an experienced partner will help assure success.
For more information on this topic, see our blog post about the difference between a modified enclosure and a custom enclosure.
How to Make Custom Electronic Enclosures
If you are truly starting from a blank sheet of paper, then the first decision to make about your enclosure is, what kind of enclosure do I need? Enclosures come in a variety of types, styles and materials. Look at the websites of enclosure suppliers to get an idea of what’s available.
Start by asking the basic questions.
- Where will your design be used? What environmental threats should be considered?
- How strong does the enclosure need to be?
- Does the application require portability (lightweight)?
- How will the enclosure be mounted?
- Will internal heat be an issue?
- What kind of access will be required in the field?
- Are there indicators or displays that need to be read?
The answers to these questions will lead you to select a particular style and material.
Sheet metal electrical enclosures. (Aluminum and steel.) Pros: Metal dissipates heat. Strong. Easy to customize. RF shielding. Cons: Steel may corrode. Limitations in appearance, generally boxy.
Plastic electronic enclosures. Molded plastic permits any shape and texture. Popular for NEMA and IP rated enclosures. Clear covers are available with some models. Corrosion resistant.
Fiberglass electronic enclosures. Similar to plastic but stronger. Tighter dimensional tolerances. Lighter and less costly than stainless steel. High impact strength and has superior working temperatures. Chemical resistant.
Die cast aluminum electronic enclosures. Cost-effective protection. Metal dissipates heat the best. RF shielding. Strength and durability. Good for grounding.
Extruded aluminum electronic enclosures. Plastic end caps. Attractive and cost-effective, aluminum dissipates heat. Available with IR panels. Ideal for housing single PCBs.
Of course, if you need a cabinet or rack, then the only option is steel.
After you have selected the type of enclosure and its material, the next step is to determine the dimensions. Typically, engineers choose the smallest enclosure possible that will still accommodate their components and printed circuit boards. Engineers should properly plan the location of power components and signal wires. After you submit your CAD file or requirements to your custom enclosure supplier, then issues such as tolerances, mounting, and drafting angles are considered. Then the supplier will send you a CAD drawing for final approval.
Expert Advice
We hope the information in this guide to custom enclosures is helpful. To get specific advice or a quote on your next project, contact our experts at saleseast@budind.com or reach out to us on our website’s chat.